Casting Urethane - A Comprehensive Guide
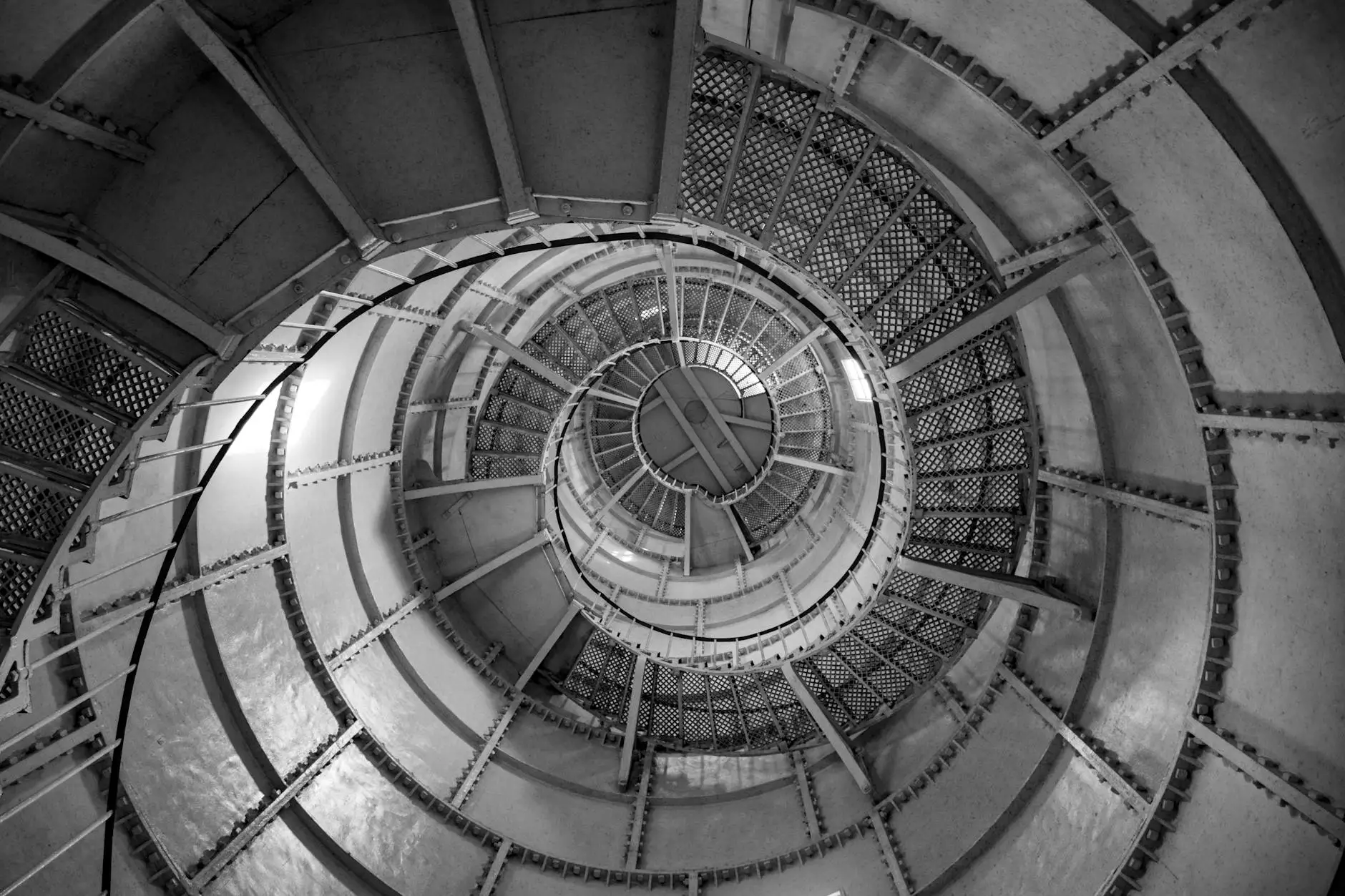
Introduction
Welcome to QuickParts.com, your go-to destination for all your manufacturing needs. In this comprehensive guide, we will dive into the fascinating world of casting urethane, a versatile and reliable manufacturing technique. Whether you are a metal fabricator or a 3D printing enthusiast, understanding the benefits and process of casting urethane can help further enhance your projects.
Why Choose Casting Urethane?
When it comes to manufacturing, selecting the right material is crucial. Casting urethane offers a myriad of benefits that make it an excellent choice for a wide range of applications. Its unique properties allow for exceptional versatility, flexibility, and durability. From creating prototypes and functional parts to producing custom molds, casting urethane excels in delivering high-quality results.
Benefits of Casting Urethane
Let's explore some of the key advantages of using casting urethane:
- Customizability: Casting urethane allows you to tailor the material to meet specific requirements, such as hardness, color, and texture. This level of customization offers endless possibilities in creating products that align with your vision.
- Cost-effective: Compared to other manufacturing methods, casting urethane provides an affordable solution without compromising on quality. The process is efficient, reducing production time and minimizing wastage.
- Strength and Durability: Urethane offers exceptional strength and durability, making it capable of withstanding various physical stresses and environmental conditions. This makes it ideal for producing parts that require long-lasting performance.
- Design Flexibility: Casting urethane enables intricate and complex designs to be replicated with precision. This allows for the creation of detailed prototypes and functional parts that closely mimic the final product, allowing for design validation and testing.
- Material Properties: Urethane can be formulated to possess a wide range of material properties, including hardness, flexibility, vibration dampening, and resistance to chemicals or UV radiation. This versatility ensures that the material can fulfill specific project requirements.
The Casting Urethane Process
Now that we understand the benefits, let's take a closer look at the casting urethane process:
Step 1: Mold Creation
The casting process begins with the creation of a mold that will shape the urethane material. The mold can be crafted using various methods such as 3D printing, CNC machining, or traditional mold making techniques. The mold design should be precise to ensure accurate and consistent results.
Step 2: Material Selection
Choosing the right urethane material is essential for the desired end product. Factors such as hardness, color, and material properties need to be considered. QuickParts.com offers a wide range of urethane materials specifically formulated to meet different application requirements.
Step 3: Preparation and Mixing
Once the mold is ready, the urethane material is prepared. It involves measuring and mixing the appropriate components according to the manufacturer's instructions. The mixture should be well-prepared to ensure uniformity and optimal performance.
Step 4: Casting
The mixed urethane material is poured or injected into the mold. Careful attention is given to avoid any air bubbles or voids, as they can impact the final product's quality and strength. The material is left to cure and solidify within the mold.
Step 5: Demolding and Finishing
After the urethane has fully cured, the mold is opened, and the part is carefully removed. Any excess material is trimmed, and the surface is finished to achieve the desired texture and appearance. QuickParts.com offers post-processing services to provide a final touch to your casting urethane parts.
Applications of Casting Urethane
The versatility and reliability of casting urethane make it applicable in various industries and sectors. Some common applications include:
- Prototyping: Casting urethane allows for rapid prototyping, enabling engineers and designers to test and finalize their designs before moving to mass production.
- Product Development: From soft-touch grips and gaskets to complex engineering components, casting urethane serves as a reliable choice for creating functional parts for product development.
- Foundry Patterns: Urethane patterns can be used to create molds for metal casting, offering a cost-efficient alternative to traditional patterns.
- Medical Devices: Urethane is often used to manufacture medical devices due to its biocompatibility and ability to meet stringent medical industry standards.
- Automotive Parts: Casting urethane is ideal for producing durable, precise, and custom automotive parts, including interior components, gaskets, and seals.
Conclusion
As we conclude this comprehensive guide on casting urethane, it's evident that this manufacturing technique offers remarkable advantages in terms of versatility, customizability, and cost-effectiveness. QuickParts.com, with its expertise in metal fabrication and 3D printing, ensures high-end urethane casting services for a wide range of applications. Whether you are looking to create prototypes, functional parts, or molds, casting urethane can meet your manufacturing needs efficiently and reliably.
Embrace the world of casting urethane and unlock endless possibilities for your business with QuickParts.com. Contact us today to discuss your unique requirements and let our team of experts help you bring your ideas to life.