Maximize Efficiency with High-Quality Bottle Label Applicators
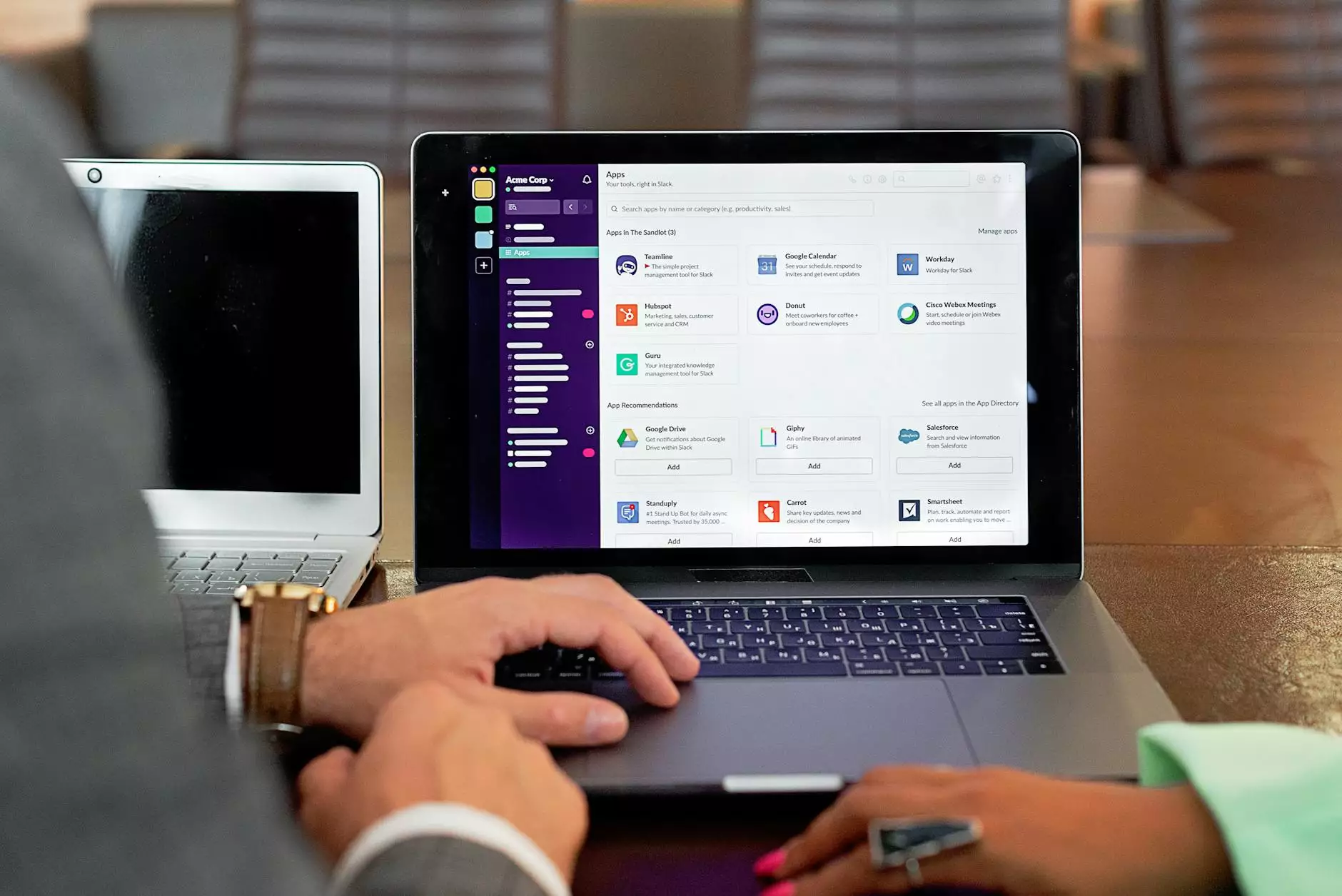
In today’s fast-paced business environment, efficiency is crucial. Manufacturers, distributors, and retailers strive for solutions that can streamline their operations and enhance productivity. One such innovative solution is the use of a bottle label applicator. This article explores the benefits, types, and considerations of using bottle label applicators in your business. Whether you are in the printing services, electronics, or computer sectors, understanding how to optimize your labeling processes can significantly impact your success.
The Importance of Labeling in Business Operations
Labeling is more than just an aesthetic addition to your products; it serves multiple essential functions, including:
- Branding: Labels represent your brand's identity and can influence consumer perception.
- Information: Labels provide necessary information, including ingredients, usage instructions, and safety warnings.
- Regulatory Compliance: Many industries have strict labeling requirements that businesses must adhere to.
- Marketing: Well-designed labels can attract customers and encourage impulse purchases.
Effective labeling is thus integral to ensuring compliance while enhancing the customer experience.
What is a Bottle Label Applicator?
A bottle label applicator is a device designed to automatically apply labels to bottles. These machines are essential in many industries, including beverage, pharmaceutical, and cosmetics. They can handle various bottle shapes and sizes, ensuring that labels are precisely placed for optimal visibility and compliance.
Benefits of Using a Bottle Label Applicator
Investing in a bottle label applicator comes with several advantages:
- Increased Efficiency: Automating the labeling process significantly reduces the time required to label products.
- Consistency: Provides uniformity in labeling, which is critical for brand recognition and customer trust.
- Cost-effective: Eliminates labor-intensive manual labeling processes, reducing labor costs over time.
- Scalability: Easily adaptable to increasing production volumes without compromising quality.
- Accuracy: Minimizes human error, ensuring that each product is labeled according to specifications.
Types of Bottle Label Applicators
There are several types of bottle label applicators available on the market, each designed for specific applications and operational needs:
1. Manual Label Applicators
These are typically used for small-scale operations where large volumes of bottles are not handled. Manual applicators enable workers to apply labels by hand, suitable for artisan producers or craft breweries.
2. Semi-Automatic Label Applicators
Semi-automatic systems require minimal manual effort. Operators manually place the bottle in position, and the machine applies the label automatically. This option is ideal for businesses looking to increase productivity while keeping costs low.
3. Fully Automatic Label Applicators
Fully automatic systems are designed for high-volume production environments. These machines can label thousands of bottles per hour, ensuring a fast and efficient labeling process. They are ideal for large manufacturers.
4. Wrap-Around Label Applicators
These applicators wrap the label around the bottle, providing full coverage. They are commonly used for cylindrical bottles and are excellent for beverages and chemicals.
5. Front and Back Label Applicators
Used for products that require a label on both the front and back, these systems can label multiple sides of a bottle in one pass. Ideal for pharmaceuticals and cosmetics that need extensive information on their packaging.
How to Choose the Right Bottle Label Applicator
Selecting the right bottle label applicator depends on several factors:
- Production Volume: Consider how many bottles you need to label daily and choose a machine that can handle that capacity.
- Label Size: Ensure that the applicator you choose can accommodate the dimensions of your labels.
- Bottle Shape: Different applicators cater to various bottle shapes, including cylindrical or square bottles.
- Budget: Determine your budget for the machinery, keeping in mind that higher-quality machines may have higher upfront costs but offer long-term savings.
- Space: Assess the layout of your production area to ensure the machine fits without disrupting workflow.
Best Practices for Operating Bottle Label Applicators
Once you invest in a bottle label applicator, implementing best practices is vital for maximizing its efficiency:
1. Regular Maintenance
Perform routine maintenance according to the manufacturer's guidelines to prevent breakdowns and ensure optimal performance. This includes cleaning, lubricating moving parts, and checking for wear and tear.
2. Use the Right Labels
Ensure that the labels you use are compatible with the applicator. Consider factors such as adhesive type, material, and print quality.
3. Train Staff
Proper training for operators is essential to minimize errors and maximize the machine’s capabilities. Ensure that your team understands how to operate and troubleshoot the applicator.
4. Monitor Production Levels
Keep track of production levels and label usage to ensure that you never run short on supplies. This also helps in making informed decisions about scaling your operations.
Conclusion: Empower Your Business with Advanced Labeling Solutions
In conclusion, a bottle label applicator is a transformative investment for businesses seeking to enhance their operational efficiency. By automating the labeling process, you will save time, reduce costs, and ensure compliance with labeling regulations. With various options available, you can select a system that aligns with your production needs and budget.
At Omega Brand, we provide insights into the latest printing services, electronics, and computer technologies that can complement your labeling solutions. Embrace the future of efficient labeling and watch your business thrive!