Ultimate Guide to Lifting Equipment Regulations for Safe and Compliant Business Operations
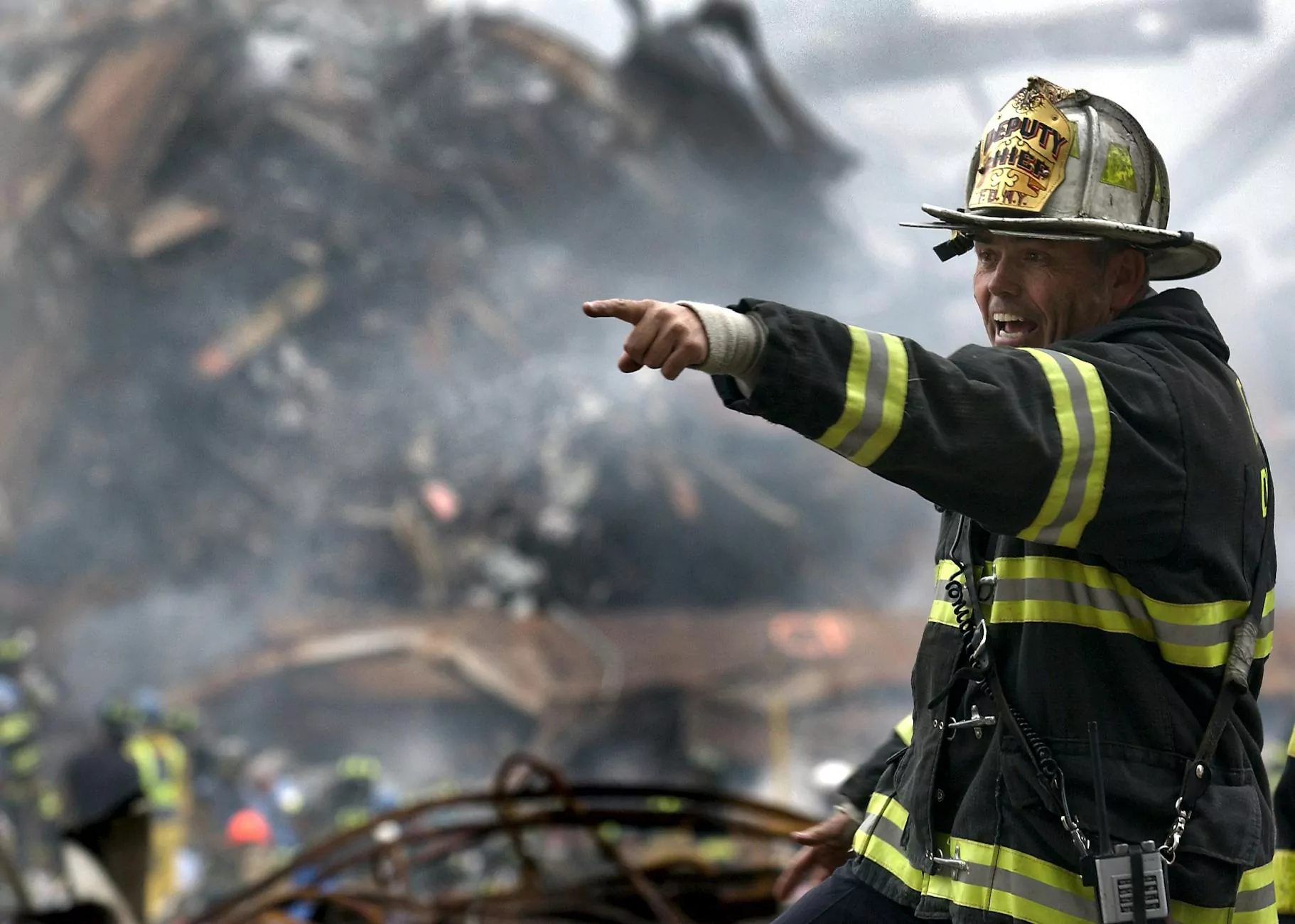
In today's fast-paced industrial and commercial environments, the importance of adhering to proper lifting equipment regulations cannot be overstated. Whether you operate within the Home & Garden sector, provide professional Gardeners services, or engage in Pest Control operations, understanding and implementing the correct safety standards for lifting equipment is paramount. This comprehensive guide provides an in-depth exploration of lifting equipment regulations, empowering your business to operate efficiently, safely, and in compliance with all legal requirements.
Understanding the Significance of Lifting Equipment Regulations
Lifting equipment regulations are designed to promote safety, minimize risks, and ensure legal compliance when handling heavy loads. These regulations serve as a framework for the proper selection, inspection, maintenance, and operation of lifting devices. For various sectors—ranging from home improvement to agricultural operations—the stakes are high; improper use or maintenance can lead to severe injuries, fatalities, and costly legal repercussions.
The Core Principles of Lifting Equipment Regulations
The lifting equipment regulations revolve around several fundamental principles to safeguard users and observers. These include:
- Design Safety: Ensuring the equipment is designed and manufactured to meet safety standards.
- Installation and Use: Proper installation and correct operational procedures.
- Inspection and Maintenance: Routine checks and preventive maintenance to identify and rectify potential issues.
- Operator Training: Ensuring operators are adequately trained and competent.
- Compliance Documentation: Keeping detailed records to demonstrate compliance.
Legal Framework Governing Lifting Equipment
To navigate the legal landscape successfully, it’s essential to familiarize yourself with the key regulations and standards. In the UK, the main legislation includes:
- LOLER (Lifting Operations and Lifting Equipment Regulations) 1998: This is the primary regulation mandating the safe use of lifting equipment. It applies extensively across sectors, including businesses involved in home improvement, gardening, and pest control when equipment such as lifts, hoists, or cranes are used.
- PUWER (Provision and Use of Work Equipment Regulations) 1998: This regulation emphasizes the suitability, maintenance, and safe use of all work equipment, including lifting devices.
- BS EN Standards and ISO Regulations: Technical standards offering detailed specifications for design, testing, and safety protocols.
Ensuring compliance with these frameworks not only mitigates legal risk but also fosters a culture of safety within the organization.
Key Components of Good Practice in Lifting Equipment Management
Maintaining a high standard of safety involves several critical practices:
- Risk Assessments: Conduct thorough risk assessments for all lifting operations, considering load weights, crane capacity, environment, and operator skills.
- Proper Equipment Selection: Choose lifting equipment that conforms to recognized standards and is suitable for the specific tasks.
- Routine Inspections: Implement scheduled inspections to identify wear, corrosion, or mechanical failures before they result in accidents.
- Regular Maintenance: Adhere to manufacturer guidelines for maintenance, calibration, and testing.
- Effective Training Programs: Ensure all relevant personnel understand the safety procedures and proper operation of lifting equipment.
- Documentation and Record-Keeping: Maintain detailed records of inspections, maintenance, and staff training for accountability and audit purposes.
Innovations and Modern Technologies Enhancing Lifting Safety
The evolving landscape of technology offers innovative solutions to enhance compliance and safety, including:
- Smart Lifting Devices: Equipped with sensors and IoT technology to monitor load, capacity, and operational health in real time.
- Digital Inspection Tools: Mobile apps and software streamline inspection routines and record-keeping.
- Automated Safety Systems: Features such as overload protection, automatic brakes, and emergency stop functions improve safety margins.
Incorporating these innovations into your business can lead to fewer accidents, improved efficiency, and demonstrates a commitment to the highest safety standards.
Benefits of Strict Compliance with Lifting Equipment Regulations
Adhering to lifting equipment regulations brings numerous advantages:
- Enhanced Safety: Protects employees, clients, and property from accidents and injuries.
- Legal Compliance: Avoids fines, legal action, and shutdowns resulting from non-compliance.
- Operational Efficiency: Properly maintained equipment minimizes downtime and prolongs lifespan.
- Reputation Management: Demonstrates your commitment to safety and professionalism to clients and partners.
- Financial Savings: Reduces costs associated with accidents, insurance claims, and equipment replacement.
Special Considerations for the Home & Garden Sector
While the Home & Garden sector may often utilize smaller lifting devices such as lifts for heavy furniture or scaffold towers, it remains crucial to adhere to the same safety principles and regulations. For gardeners and landscapers:
- Use of portable lifts and hoists must be inspected and maintained regularly.
- Operators should be trained to recognize load limits and environmental hazards.
- Proper storage and setup prevent accidental tipping or collapse.
Applying stringent safety standards ensures projects remain safe, timely, and compliant.
Training and Certification: Building a Safety-Centric Workforce
Essential to ongoing compliance is a well-trained workforce. Training programs should cover:
- Understanding lifting equipment regulations and legal responsibilities.
- Proper operation and maneuvering techniques.
- Emergency procedures and accident prevention measures.
- Inspection and maintenance routines.
Certification from recognized bodies enhances credibility and demonstrates due diligence.
Conclusion: Ensuring Long-Term Success Through Safety and Compliance
The importance of lifting equipment regulations in maintaining a safe, compliant, and efficient business cannot be overstated. By proactively implementing these standards, your organization will not only protect its personnel and assets but also position itself as a leader in safety excellence within the Home & Garden, Gardening, and Pest Control sectors. Remember, safety is an ongoing process that evolves with emerging technologies, industry standards, and regulatory updates.
Embrace a culture of continuous improvement, prioritize thorough training, conduct regular inspections, and stay informed about legislative changes. Doing so will ensure your business remains resilient, reputable, and ready to meet future challenges with confidence.
For expert guidance, safety equipment, and compliance support tailored to your specific industry needs, trust safeplantuk.co.uk. We are dedicated to enhancing safety standards and operational efficiencies for businesses across the UK.