Revolutionizing Construction with the Best Volumetric Concrete Plant Solutions
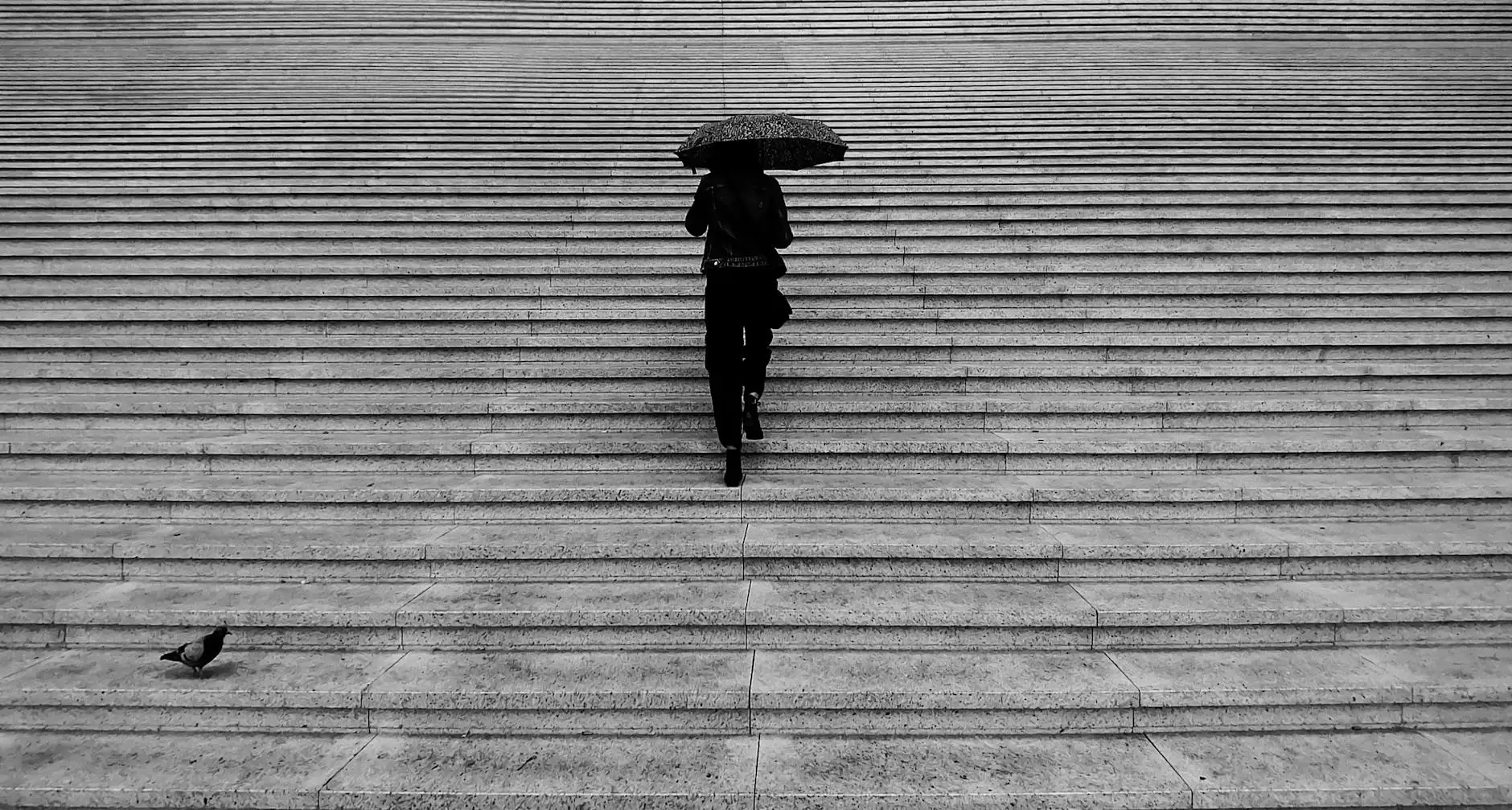
In the ever-evolving landscape of modern construction, efficiency, precision, and sustainability are paramount. The introduction of advanced volumetric concrete plant technology has transformed how construction companies approach concrete production, offering tailored, on-demand solutions that meet diverse project requirements. This innovative approach not only boosts productivity but also ensures superior quality control and environmental friendliness, positioning it as a cornerstone of future-ready construction practices.
What Is a Volumetric Concrete Plant?
A volumetric concrete plant is a sophisticated, mobile concrete batching system that combines raw materials—aggregates, cement, water, and admixtures—on-site in precisely controlled proportions. Unlike traditional concrete mixers that deliver pre-mixed concrete from a central plant, volumetric plants allow for real-time mixing, providing freshly made concrete exactly when and where it is needed.
This technology employs advanced volumetric measurement systems and computer controls to accurately dispense materials, ensuring consistent quality, customizable mixes, and minimal waste. The mobility and flexibility of these plants make them ideal for various construction environments, from urban developments to remote infrastructure projects.
Advantages of Using a Volumetric Concrete Plant
1. Unmatched Flexibility and Precision
One of the most significant advantages of the volumetric concrete plant is its ability to produce multiple concrete mixes with different specifications on a single site. This flexibility enables contractors to change mix designs on the fly, based on real-time project needs, without waiting for deliveries or multiple batching units.
- Customizable Mixes: Adjust water-to-cement ratios, additives, and aggregate proportions swiftly.
- Immediate Production: Mix concrete precisely when needed, drastically reducing queues and delays.
- Reduced Waste: Only the required amount of concrete is produced, minimizing surplus and disposal costs.
2. Enhanced Quality Control
Continuous on-site mixing allows for stringent quality assurance. Real-time monitoring of materials and mixing parameters ensures that each batch adheres to specified standards, resulting in high-strength, durable concrete that improves the longevity and safety of structures.
The ability to adjust mixes during production further guarantees optimal results, especially in projects requiring specific properties such as high early strength, workability, or sulfate resistance.
3. Cost-Efficiency and Time Savings
Utilizing a volumetric concrete plant reduces logistical expenses associated with transporting concrete. As the plant is mobile, it eliminates the need for repeated deliveries and waiting times, streamlining the workflow and compressing project timelines.
Contractors benefit from lower labor costs and less material waste, significantly increasing overall project profitability.
4. Environmental Benefits
Environmental sustainability is a critical consideration in modern construction. Volumetric plants contribute positively by minimizing waste, reducing transportation emissions, and enabling precise use of raw materials. Additionally, on-site mixing reduces carbon footprint associated with concrete logistics.
This aligns with green building initiatives and helps construction firms meet regulatory standards for environmental responsibility.
Applications of a Volumetric Concrete Plant in Construction
The versatility of volumetric concrete plants makes them suitable for a broad range of applications, including:
- Residential and Commercial Buildings: Precise concrete for foundation, slab, and structural components.
- Infrastructure Projects: Roads, bridges, tunnels, and railways benefit from quick, on-site concrete production.
- Precast and Prefabricated Elements: Controlled mixing promotes high-quality, consistent products stored for assembly.
- Remote and Hard-to-Access Locations: Mobile setup allows for immediate concrete production without significant infrastructure.
- Rapid Repairs and Emergency Construction: Instantaneous production capability accelerates repair work, reducing disruptions.
Key Components of a Modern Volumetric Concrete Plant
To understand the capabilities and quality of a volumetric concrete plant, it is essential to recognize its primary components:
- Material Bins and Hoppers: Storage units for aggregates, cement, and admixtures with precise dispensing mechanisms.
- Mixing Chamber: The core unit where materials combine and are thoroughly mixed to produce uniform concrete.
- Computer Control System: Advanced software that automates measurement, mix design, and production parameters.
- Mobile Frame and Transportation: Robust chassis and wagons enabling easy relocation across construction sites.
- Water Supply System: On-demand water addition with accurate control for immediate mixing.
Technological Innovations in Volumetric Concrete Plant Design
Recent technological advances have propelled volumetric concrete plant capabilities, emphasizing automation, durability, and environmental resilience:
- Smart Control Software: Integration with IoT devices for remote monitoring and data collection to optimize operations.
- High-Precision Dispensers: Load cells and sensors ensure accurate material ratios, reducing variability.
- Eco-Friendly Materials and Processes: Incorporation of supplementary cementitious materials and water reclamation systems.
- Modular Design: Components designed for quick assembly, repair, and upgrading, ensuring long-term usability.
Choosing the Right Volumetric Concrete Plant Provider
Selecting an experienced and reputable supplier such as polygonmach.com ensures access to cutting-edge technology, comprehensive after-sales support, and customizable solutions suited to your specific project needs.
When evaluating options, consider factors such as:
- Technological Features: Automation, remote control, and material handling capabilities.
- Mobility and Size: Suitability for your project scale and logistical constraints.
- Build Quality and Durability: Robust construction for harsh environments.
- Support and Maintenance: Availability of technical support and spare parts.
- Cost and Return on Investment: Overall affordability and efficiency gains.
Future Trends in Volumetric Concrete Plant Technology
As the construction industry continues to evolve, the future of volumetric concrete plants is focused on increasing automation, integrating artificial intelligence, and enhancing environmental sustainability. Key trends include:
- Integration with Building Information Modeling (BIM): Facilitating seamless project planning and real-time adjustments.
- Advanced Material Compatibility: Ability to handle innovative concrete formulations such as ultra-high-performance concrete (UHPC).
- Autonomous Operation: Fully automated plants capable of operating with minimal human intervention.
- Green Technologies: Use of recycled materials and energy-efficient processes to reduce carbon footprint.
Conclusion: Embracing the Power of Volumetric Concrete Plant for Future Construction
Investing in a volumetric concrete plant marks a strategic move towards a smarter, more sustainable, and highly efficient construction process. By leveraging the latest technological innovations, construction companies can achieve higher quality standards, reduce costs, and improve project timelines—making this technology indispensable for modern infrastructure development.
For businesses aiming to stay ahead in competitive markets, partnerships with leading suppliers like polygonmach.com provide access to superior equipment, expert support, and customized solutions that transform your project execution.
In summary, the adoption of the volumetric concrete plant signifies not just an operational upgrade, but a significant step towards innovative, eco-friendly, and profitable construction practices that will shape the future of the industry.